Advanced Welding WPS: Tailoring Requirements for Facility Jobs
Advanced Welding WPS: Tailoring Requirements for Facility Jobs
Blog Article
Unlocking the Power of Welding WPS: Approaches for Effectiveness and Safety And Security in Fabrication
In the realm of fabrication, Welding Procedure Requirements (WPS) stand as the foundation of welding operations, determining the necessary actions for accomplishing both performance and safety in the construction procedure. Understanding the intricacies of WPS is paramount to using its full possibility, yet several companies battle to open real power that exists within these papers (welding WPS). By delving right into the methods that optimize welding WPS, a world of boosted efficiency and heightened safety waits for those ready to discover the nuances of this crucial aspect of fabrication

Relevance of Welding WPS
The value of Welding Treatment Requirements (WPS) in the manufacture sector can not be overemphasized. WPS offer as an essential roadmap that details the essential actions to ensure welds are done constantly and appropriately. By specifying necessary specifications such as welding procedures, products, joint styles, preheat temperatures, interpass temperature levels, filler metals, and post-weld heat treatment demands, WPS offer a standard method to welding that enhances performance, high quality, and security in manufacture processes.
Adherence to WPS aids in accomplishing uniformity in weld quality, decreasing the chance of problems or structural failings. This standardization additionally helps with conformity with sector guidelines and codes, making certain that made frameworks fulfill the required safety standards. Moreover, WPS documentation allows welders to reproduce successful welding procedures, resulting in consistent outcomes throughout various jobs.
Fundamentally, the meticulous advancement and strict adherence to Welding Procedure Requirements are vital for maintaining the honesty of bonded structures, safeguarding against prospective risks, and supporting the credibility of fabrication firms for providing high-grade product or services.
Key Components of Welding WPS
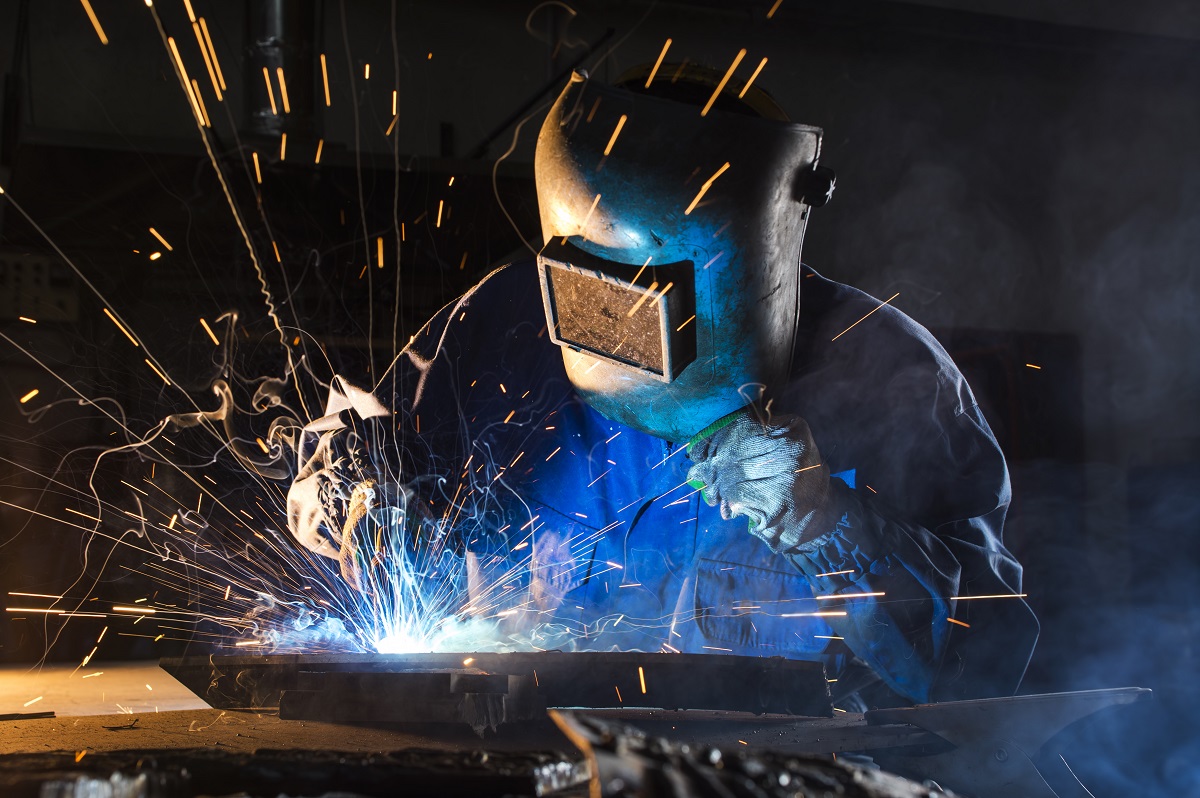
Enhancing Efficiency With WPS
When maximizing welding operations, leveraging the essential aspects described in Welding Procedure Specifications (WPS) comes to be crucial for simplifying processes and optimizing performance. One means to boost efficiency with WPS is by very carefully picking the ideal welding specifications.
Regularly examining and updating the WPS to integrate any type why not try this out of lessons learned or technical developments can also add to effectiveness improvements in welding procedures. By embracing the standards set forth in the WPS and continuously seeking means to optimize procedures, producers can accomplish higher efficiency levels and premium end results.
Ensuring Safety And Security in Manufacture
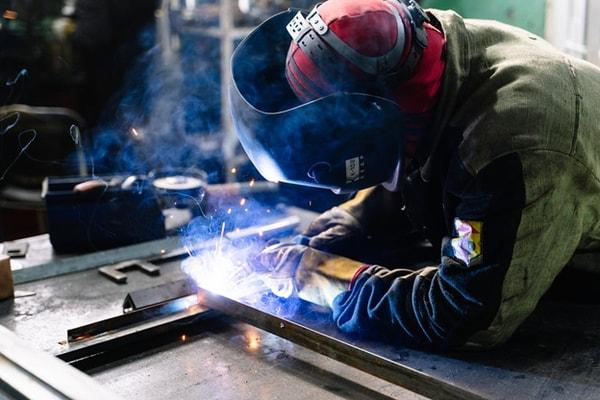
Safety methods in manufacture play an essential function in safeguarding employees and enhancing functional treatments. Guaranteeing safety in construction includes a diverse method that includes different elements of the welding process. One fundamental aspect is the provision of individual protective devices (PPE) tailored to the particular hazards existing in the fabrication environment. Welders should be furnished with ideal equipment such as learn the facts here now headgears, handwear covers, and protective clothes to alleviate threats associated with welding activities.
Moreover, adherence to correct ventilation and fume removal systems is vital in preserving a healthy job atmosphere. Welding fumes contain dangerous substances that, if breathed in, can position significant health and wellness threats. Applying reliable air flow actions assists to decrease exposure to these unsafe fumes, advertising respiratory health among workers.
Routine tools maintenance and examinations are also crucial for guaranteeing safety and security in manufacture. Damaged machinery can cause injuries and crashes, highlighting the importance of routine checks and timely repairs. By focusing on precaution and promoting a culture of recognition, fabrication facilities can create a protected and effective workplace for their workers.
Executing WPS Ideal Practices
To enhance operational efficiency and make certain quality results in fabrication processes, including Welding Procedure Requirements (WPS) best methods is vital - welding WPS. Carrying out WPS finest methods includes meticulous planning, adherence to sector standards, and continuous monitoring to ensure ideal outcomes. First of all, choosing the suitable welding process, filler material, and preheat temperature level defined in the WPS is critical for attaining the wanted weld top quality. Second of all, guaranteeing that qualified welders with the required qualifications execute the welding procedures according to the WPS guidelines is essential for consistency and dependability. Regularly assessing and updating WPS records to mirror you could try these out any procedure enhancements or changes in products is likewise a vital ideal practice to preserve precision and significance. Additionally, giving extensive training to welding employees on WPS demands and ideal practices cultivates a culture of security and high quality within the construction environment. By vigilantly applying WPS ideal practices, fabricators can enhance their operations, lessen errors, and supply exceptional products to satisfy customer assumptions.
Verdict
Finally, welding WPS plays a critical role in making sure efficiency and security in fabrication processes. By concentrating on crucial elements, enhancing performance, and carrying out ideal techniques, companies can enhance their welding procedures. It is important to prioritize precaution to avoid mishaps and make certain a smooth manufacturing process. By complying with these methods, organizations can unlock the full capacity of welding WPS in their construction procedures.
In the realm of manufacture, Welding Procedure Specifications (WPS) stand as the backbone of welding operations, dictating the required steps for achieving both performance and safety and security in the manufacture procedure. By specifying vital specifications such as welding processes, materials, joint designs, preheat temperatures, interpass temperatures, filler metals, and post-weld warm treatment requirements, WPS provide a standard technique to welding that improves efficiency, high quality, and safety and security in construction procedures.
When enhancing welding procedures, leveraging the essential aspects outlined in Welding Procedure Specifications (WPS) comes to be essential for optimizing and improving processes performance. (welding WPS)
Report this page